Содержание
Что относится к легким металлам
Металлопрокат в розницу и оптом. Металлобаза в Москве
Наша продукция
/images/bullet.gif”/>Квадрат
/images/bullet.gif”/>Катанка
/images/bullet.gif”/>Арматура
/images/bullet.gif”/>Круг стальной
/images/bullet.gif”/>Уголки стальные
/images/bullet.gif”/>Полоса стальная
/images/bullet.gif”/>Сетка кладочная
/images/bullet.gif”/>Листовой прокат
/images/bullet.gif”/>Трубы профильные
/images/bullet.gif”/>Швеллер стальной
/images/bullet.gif”/>Электроды монолит
В группу легких металлов включаются металлы с плотностью ρ до 4,5 г/см3. Легкими металлами, важнейшими для технического применения (преимущественно как основа сплава), являются Al, Mg, Ti и Be. Если даже Al-сплавы по распространению представляют наиболее значительную группу среди легких металлов, то все же для специфических целей применения предлагают материалы Ti и Be, комплексы свойств которых заслуживают внимания для будущих разработок материалов. Магниевые сплавы уже очень давно нашли техническое применение, например, в строительстве дирижаблей и самолетов, но из-за их проблематичной обрабатываемости и их воспламеняемости были вытеснены. Очень незначительная плотность (ρ = 1,74 г/см3) снова выдвигает в последнее время магний как основу сплава на передний план.
В актуальном развитии сплавы Al-Li из-за своей легкости и хороших прочностных качеств пользуются все большим вниманием.
В мировом потреблении алюминия, %, наиболее интенсивно участвует упаковочная промышленность, особенно для банок с напитками:
В машиностроении наряду со сталью алюминий со своими сплавами стал одним из важнейших конструкционных материалов. Соответственно велико многообразие алюминиевых сплавов, которые соответствуют большому количеству необходимых требований. Рациональное разделение сплавов производится на литейные и деформируемые. Оба типа сплавов можно разделить на способные и не способные к дисперсионному твердению сплавы.
Алюминий не проявляет аллотропного преобразования, т.е. в противоположность к стали он не подвержен наклепу в результате фазового превращения., В качестве мер для повышения прочности этого материала могут применяться:
– наклеп;
– упрочнение легированием (упрочнение твердого раствора добавками и многофазностью);
– дисперсионное твердение (старение).
Так как стареющие алюминиевые сплавы, в частности типа AlCuMg, для достижения оптимальных характеристик требуют хорошего измельчения, то применяется термообработка для дисперсионного старения преимущественно у деформируемых сплавов; она пригодна также при высокопрочных качествах отливки для улучшения прочностных характеристик.
Литейные сплавы. К самым важным техническим литейным сплавам относятся сплавы Al-Si. Система Al-Si образует простую эвтектическую систему с эвтектической точкой при 11,7 % Si и 577 °C (рис. 9.4.29). Близкие к эвтектическим сплавы с содержанием от 11 до 13 % Si известны также как силуминовое литье. При медленном охлаждении (литье в песчаные формы) заэвтектического сплава с 13 % Si первично выделяющийся твердый раствор Si образует большие, угловатые, пластинчатые в шлифе, преимущественно игольчатые кристаллы. Эта неблагоприятная структура ведет к ярко выраженной хрупкости таких сплавов (рис. 9.4.30).
Нежелательной хрупкости можно избежать благодаря так называемому облагораживанию металлов. Путем добавки примерно 0,1 % Na при 720—780 °C в плавку неблагоприятно деформируемые кристаллы кремния очищаются, округляются и образуют тонкодиспергированную эвтектику (рис. 9.4.31). Эвтектическая температура снижается благодаря добавлению Na от 577 до 564 °C, причем эвтектическая концентрация сдвигается на 14 %. Заэвтектический сплав затвердевает, таким образом, доэвтектически, причем натрий, кроме того, вероятно, затормаживает диффузию.
При быстром охлаждении, которое существует в кокильном литье, достигается действие, подобное действию при облагораживании металлов. Здесь также сдвигается эвтектическая точка с помощью переохлаждения. Возникает очень чистая эвтектическая структура, так что при кокильном литье можно отказаться от облагораживания металлов натрием (см. рис. 9.4.29).
Предел прочности при растяжении необлагороженного литья в песчаные формы составляет от 100 до 120 Н/мм2. Он повышается благодаря облагораживанию металлов натрием до 240 Н/мм2 при показателях удлинения от 10 до 15 %. В кокильном литье прочность сплава составляет с 13 % Si до 260 Н/мм2.
Для поршневых сплавов повышается содержание Si и добавляется Cu. Маркированный поршневой сплав имеет 25 % Si и 5 % Cu.
Содержание меди в таких сплавах может увеличиваться до 14 %. Уже 1 % Cu повышает предел прочности при растяжении алюминия от 140 до 210 Н/мм2.
Особое значение имеет Cu при более высоком содержании для стареющих деформируемых алюминиевых сплавов. Для поршневых сплавов важна незначительная величина усадки — только 1,2%. Другим важным легирующим злементом для Al вообще, но особенно для литейных сплавов, является Mg (до 10 %). Такие сплавы отличаются хорошей устойчивостью против коррозии. Следует еще упомянуть легирующие элементы Mn (до 15 %), Zn (до 6 %), а также в небольших количествах Cr (до 0,4 %) и Ti (до 0,3 %).
Сплавы AlMn все шире применяются вместо чистого алюминия, так как эти сплавы объединяют очень хорошую устойчивость против коррозии с прочностью, более высокой по сравнению с чистым алюминием.
Деформируемые сплавы. Содержание легирующих составных частей, а также примесей в деформируемых сплавах в целом меньше, чем в литейных. В то время как литейные сплавы часто производятся с применением скрапа (вторичные сплавы), повышенные требования к деформируемым сплавам требуют преимущественно их выплавки из металлургического алюминия (первичные сплавы). Нестареющими деформируемыми сплавами являются AlMg-сплавы, у которых высокая твердость из-за легирования и прочность не уменьшаются от отжига и сварки. Принципиально диаграмма состояния AlMg-сплавов с уменьшающейся, растворимостью Mg в Al при снижении температуры имеет необходимые предпосылки к дисперсионному твердению (рис. 9.4.32). Однако здесь оказывается, что эти необходимые предпосылки сами по себе еще недостаточны, а что вид форма выделения при распаде играют существенную роль. К этой группе не способных к дисперсии сплавов относятся AlMn-сплавы с содержанием Mn до 2 %. Более высокого содержания Mn избегают из-за выделения повышенно хрупких А16Мn-кристаллов.
Возможность повышения прочности алюминиевых сплавов благодаря механизму старения металла значительно расширяет область применения этой группы материалов и придает обработке дисперсионным твердением такое же значение, каким обладает изменение твердости в результате фазового превращения у железных материалов, но особенно у стали. Важные подвергающиеся старению сплавы принадлежат к типу AlSi. Нестареющие AlMg-сплавы становятся стареющими вследствие добавок Cu (дюралюминий), Si и Zn.
Новое поколение высокопрочных Al-сплавов представляют Al—Li-силавы например Al—Li—Cu—Mg-сплавы, способные к дисперсии.
Литий является самым легким металлом вообще, его плотность составляет только 20 % плотности алюминия. По сравнению с обычными высокопрочным А1-сплавами Al—Li-сплавы примерно на 10 % легче. Вместе с более высокой (на 10 %) жесткостью можно достигнуть экономии массы на 15 % в конструкционной детали. У аэробусов такие сплавы конкурируют с углеродоволокнистыми комбинированными материалами. Более новые разработки благодаря сильному легированию сплавов типа Al—Li-материалов позволяют избежать незначительной вязкости и раннего образования трещин.
Механизм дисперсионного твердения, термообработка и достигаемое повышение прочности обсуждаются на примере группы AlCu-сплавов в разделе 13.3. Многократно сплавляемые подвергнутые дисперсионному твердению Al-сплавы достигают по прочности уровня высококачественных сталей.
Спеченный алюминиевый порошок (САП) (SAP). Изготовленные из Аl-порошка спеченные материалы обеспечивают набор требований, которые нельзя достигнуть с помощью обычных алюминиевых сплавов. Спеченный материал, состоящий из чистого Al-порошка, содержит от 6 до 14 % тонкого поверхностного слоя Al2O3, который размещается вокруг мельчайших зерен порошка. Порошок из сплава алюминия с Fe и Cr, а также 0,5 % Al2O3 превосходит по пределу термической текучести даже Ti в области от 300 до 500 °С. Этот материал применяется для лопастей компрессоров, теплообменников, а также в ядерных реакторах.
Самыми важными легирующими элементами для магния, который не пригоден в чистом виде как конструкционный материал, являются Al, Mn и/или Zn. Затвердевающий в гексагональной структуре Mg плохо деформируется в холодном состоянии и имеет неблагоприятную устойчивость против коррозии. Вместе с Zn посредством дальнейшего легирования от 0,5 до 0,7 % Zr и Ce достигаются беспористая отливка, измельчение зерна и благодаря этому улучшенная деформируемость. Благодаря Th повышается жаропрочность. Новые разработки связаны с литейными сплавами Mg-Y, которые имеют очень хорошую механическую твердость, около 290 Н/мм2, последняя снижается при 300 °C только до примерно 200 Н/мм2.
Различные магниевые сплавы известны под названием “электрон”. Магниевая отливка имеет благоприятное отношение Rm к р. По сравнению с серым литьем при применении магниевой отливки образуется экономия массы от 60 до 80 %, а в отличие от высококачественного алюминиевого литья всегда создается экономия от 15 до 20 %. Деформируемые сплавы, например, с 8 % Cd, 6 % Al, 2 % Zn, достигают при горячей или холодной прокатке прочности Rm≥4000 Н/мм2.
Из-за ограниченной устойчивости против коррозии и трудностей при обработке применение Mg-сплавов сегодня ограничивается менее сильнонагруженными деталями, такими как корпус и покрытие.
Из диаграммы состояния (рис. 9.4.33) можно было бы ожидать до содержания сплава 10% Al структуру из первичных δ-твердых растворов с γ-сегрегациями. Благодаря незначительной скорости диффузии появляются, однако, нарушения , равновесия, так что также сплавы с менее чём 12,6 % Al показывают (δ+γ-эвтектику вырожденной формы. Кристаллы Al2Mg3 образуют характерные пластины, которые создают структуру, подобную перлитному эвтектоиду у стали. Длительный отжиг вблизи линии растворимости приводит фазу Al2Mg3 к столбчатому выделению на плоскости базиса (0001) гексагональных δ-твердых растворов.
Титан является невзаимодействующим и используется как плакирующий материал в строительстве химических установок. Он отличается высокой устойчивостью против коррозии, окисляющих водных коррозионных сред. Высокая антикоррозийность образуется вследствие очень стабильного пассивированного оксидного слоя, который может быстро образоваться при слабых средствах окисления.
Титановые сплавы отличаются высокой прочностью, прежде всего высокой жаропрочностью. Титановые сплавы с соответствующей термообработкой достигают прочности от 1200 до 1400 Н/мм2. Титановые сплавы применяются до температуры 500 °С, а кратковременно даже до 1000 °C и, таким образом, заполняют пробел между Al-сплавами, которые применяются до примерно 150 °C, и жаропрочными сталями.
Очень благоприятное отношение прочности на разрыв к плотности Rm/p делает титановый сплав весьма подходящим для облегченных деталей конструкций, подвергающихся сильной нагрузке, как это можно наглядно видеть на примере шатуна для высокомощного двигателя.
Высокая цена, обусловленная дорогостоящим производством титана, противостоит широкому применению, которое имеется у Al-сплавов, но при легких конструкциях он часто выгоднее прочных и очень высокопрочных сталей.
Как и железо, титан также обладает аллотропным превращением. До температуры 882 °C титан обладает гексагональной структурой, выше нее — о.ц.к. β-структурой с уменьшенным на 0,55 % объемом. Как и для стали, легирующие элементы для титана можно разделить на те, которые стабилизируют; α-структуру, и те, которые расширяют область β-фазы. Гексагональная; α-структура обладает ограниченной деформируемостью, которая при высоких температурах благодаря склонности к восприятию Н, O и N уменьшается дальше. Модуль E сравнительно незначителен.
Наряду с Al важнейшими легирующими элементами в технических титановых сплавах являются V, Sn, Mo, Zr, Nb. и Cr. Al стабилизирует β-фазу и его содержание составляет у технических сплавов ниже 10 %. Структуры технических титановых сплавов имеются в виде α-, (α + β)- или β-структуры, иногда с интерметаллическими соединениями. Очень различающаяся растворимость легирующих элементов в β- и α-фазе создает благодаря превращению перенасыщенный a-твердый раствор, который можно упрочнить путем отжига.
Чрезвычайно благоприятное отношение Rm/p и очень высокая теплоемкость вызывают определенный интерес к бериллию для особых целей. Бериллий имеет в 1,5 раза большую жесткость, чем сталь. Тормозные диски из бериллий вследствие высокой теплоемкости при одинаковых условиях остаются существенно более холодными, чем диски из стали. Если при одинаковых опытных условиях температура диска из стали после двухминутной тормозной нагрузки достигает 560 °С, то диска из бериллия — лишь 390 °C.
Однако гексагональный бериллий имеет склонность к крупнокристаллическому затвердеванию. Он чрезвычайно хрупок и имеет структурно обусловленную четко выраженную анизотропию. В агломерированной чистой форме, однако, можно хорошо осуществлять горячую деформацию. В воздухоплавании b космоплавании применяются сплавы бериллия с примерно 25 % Al, Mg и Si.
В строительстве реакторов бериллий имеет значение из-за нейтронной проницаемости.
Бериллиевые окна применяются в рентгенотехнике и рентгеноаналитике, так как они поглощают лишь малое ионизирующее излучение. Как легирующий материал бериллий используется в медных материалах для изготовления высокообжигаемых литейных и деформируемых сплавов. Для материалов с бериллием, однако, установлены четкие границы применяемости из-за его вреда здоровью и окружающей среде. Бериллиевая пыль чрезвычайно ядовита и ведет к заболеваниям легких и кожным повреждениям. (Подобные границы необходимо соблюдать также при применении тяжелых металлов, в частности кадмия, обладающего очень большой антикоррозионной устойчивостью, но ядовитость его нельзя недооценивать.)
Цветные металлы: список, названия, классификация и использование
Ведущей отраслью в экономике нашей страны является металлургия. Для успешного ее развития нужно много металла. В данной статье речь пойдет о цветных тяжелых и легких металлах и их использовании.
Классификация цветных металлов
В зависимости от физических свойств и назначения, они подразделяются на такие группы:
- Легкие цветные металлы. Список этой группы большой: в ее состав входит кальций, стронций, цезий, калий, а также литий. Но в металлургической промышленности чаще всего используются алюминий, титан и магний.
- Тяжелые металлы пользуются большой популярностью. Это всем известные цинк и олово, медь и свинец, а также никель.
- Благородные металлы, такие как платина, рутений, палладий, осмий, родий. Золото и серебро широко применяются для изготовления украшений.
- Редкоземельные металлы – селен и цирконий, германий и лантан, неодим, тербий, самарий и другие.
- Тугоплавкие металлы – ванадий и вольфрам, тантал и молибден, хром и марганец.
- Малые металлы, такие как висмут, кобальт, мышьяк, кадмий, ртуть.
- Сплавы – латунь и бронза.
Легкие металлы
Они имеют широкое распространение в природе. Эти металлы обладают маленькой плотностью. У них высокая химическая активность. Они представляют собой прочные соединения. Металлургия этих металлов начала развиваться в девятнадцатом веке. Их получают путем электролиза солей в расплавленном виде, электротермии и металлотермии. Легкие цветные металлы, список которых имеет много пунктов, используются для производства сплавов.
Алюминий
Относится к легким металлам. Имеет серебристый цвет и точку плавления около семисот градусов. В промышленных условиях используется в сплавах. Он применяется везде, где нужен металл. У алюминия плотность низкая, а прочность – высокая. Этот металл легко режется, пилится, сваривается, сверлится, паяется и сгибается.
Сплавы образует с металлами различных свойств, такими как медь, никель, магний, кремний. Они обладают большой прочностью, не ржавеют при неблагоприятных погодных условиях. У алюминия высокая электро- и теплопроводность.
Магний
Он относится к группе легких цветных металлов. Имеет серебристо-белый цвет и пленочное окисное покрытие. Обладает маленькой плотностью, хорошо обрабатывается. Металл устойчив к воздействию горючими веществами: бензином, керосином, минеральными маслами, но подвержен растворению в кислотах. Магний не магнитен. Обладает низкими упругими и литейными свойствами, подвергается коррозии.
Титан
Это легкий металл. Он не магнитен. Имеет серебристый цвет с отливом голубоватого тона. Обладает высокой прочностью и устойчивостью к коррозии. Но у титана маленькая электропроводность и теплопроводность. Теряет механические свойства при температуре 400 градусов, приобретает хрупкость при 540 градусах.
Механические свойства титана повышаются в сплавах с молибденом, марганцем, алюминием, хромом и другими. В зависимости от легирующего металла, сплавы имеют разную прочность, среди них есть и высокопрочные. Такие сплавы применяются в самолетостроении, машиностроении, судостроении. Из них производят ракетную технику, бытовые приборы и многое другое.
Тяжелые металлы
Тяжелые цветные металлы, список которых весьма широк, получают из сульфидных и окисленных полиметаллических руд. В зависимости от их типов, методы получения металлов отличаются по способу и сложности производства, в процессе которого должны полностью извлекаться ценные составляющие сырья.
Металлы этой группы бывают гидрометаллургическими и пирометаллургическими. Полученные любым методом металлы называются черновыми. Они подвергаются процедуре рафинирования. Только после этого их можно использовать в промышленных целях.
Цветные металлы, список которых представлен выше, в промышленности используются не все. В данном случае речь идет о распространенном тяжелом металле – меди. У нее высокая теплопроводность, электропроводность и пластичность.
Сплавы меди нашли широкое применение в такой отрасли промышленности, как машиностроение, а все благодаря тому, что этот тяжелый металл хорошо сплавляется с другими.
Он тоже представляет цветные металлы. Список названий большой. Однако далеко не все тяжелые цветные металлы, к которым относится цинк, используются в промышленности. Этот металл хрупкий. Но если нагреть его до ста пятидесяти градусов, он будет без проблем коваться и с легкостью прокатываться. У цинка высокие антикоррозионные свойства, но он поддается разрушению при воздействии щелочью и кислотой.
Свинец
Список цветных металлов будет неполным без свинца. Он серого цвета с проблеском голубого оттенка. Температура плавления составляет триста двадцать семь градусов. Он тяжелый и мягкий. Хорошо куется молотком, при этом не твердеет. Из него выливают различные формы. Устойчив к воздействию кислот: соляной, серной, уксусной, азотной.
Латуни
Это сплавы из меди и цинка с добавлением марганца, свинца, алюминия и других металлов. Стоимость латуни меньше, чем меди, а прочность, вязкость и коррозионная стойкость – выше. У латуни хорошие литейные свойства. Из нее производят детали путем штамповки, раскатки, вытяжки, вальцовки. Из этого металла делают гильзы для снарядов и многое другое.
Использование цветных металлов
Цветными называют не только сами металлы, но и их сплавы. Исключение составляет так называемый “чермет”: железо и, соответственно, его сплавы. В странах Европы цветные металлы носят название нежелезистых. Цветные металлы, список которых немаленький, нашли широкое применение в разных отраслях во всем мире, в том числе и в России, где являются основной специализацией. Производятся и добываются на территориях всех регионов страны. Легкие и тяжелые цветные металлы, список которых представлен большим разнообразием наименований, составляют отрасль промышленности под названием «Металлургия». Это понятие включает в себя добычу, обогащение руд, выплавку как металлов, так и их сплавов.
В настоящее время отрасль цветной металлургии получила широкое распространение. Качество цветных металлов очень высокое, они отличаются долговечностью и практичностью, применяются в строительной индустрии: ими отделывают здания и сооружения. Из них производят профильный металл, проволоку, ленты, полосы, фольгу, листы, прутки различной формы.
Легкие цветные металлы
Общее определяющее свойство любых продуктов цветной металлургии – полное либо крайне низкое содержание железа в их составе. Этим обусловлена способность таких элементов или сплавов на их основе образовывать оксидную защитную пленку и проявлять высокую стойкость к коррозии. Благодаря данному качеству изделия, изготовленные из данных материалов, обретают дополнительную функциональную ценность, находят широкое применение в различных отраслях промышленности и быту.
Группа легких цветных металлов
К наиболее распространенным способам классификации цветмета по его физико-химическим свойствам относится распределение на семь групп, среди которых выделяются так называемые тяжелые и легкие цветные металлы. Данное условное определение основано на показателе плотности материала. В основной список входят алюминий, магний, титан, литий, олово, бериллий. К этой же группе относятся кадмий, таллий, галлий, висмут, индий и другие элементы. Производство легких сплавов является крайне энергозатратным, поэтому предприятия, специализирующиеся на этой области металлургии, размещаются непосредственно вблизи источников дешевой энергии.
Специфические особенности
Несмотря на принадлежность к общей группе, разные легкие цветные металлы имеют специфические свойства, отличающие их друг от друга, а также обуславливающие ценность конкретного материала и область его применения. Чтобы лучше понять эти нюансы, стоит подробнее рассмотреть основных представителей данного вида цветмета.
Пожалуй, наиболее типичным примером легкого цветного металла, хорошо знакомого самому обширному кругу пользователей, является алюминий. Материал пластичен и легко обрабатывается, за счет чего чрезвычайно популярен в широчайшем спектре производств – от космической и авиационной промышленности до изготовления кухонной посуды. Окисная пленка надежно защищает поверхность алюминиевых изделий от негативного воздействия окружающей среды, агрессивных веществ. К главным свойствам относятся:
- высокая тепло- и электропроводность;
- стойкость к коррозии;
- высокая пластичность;
- малая плотность.
В отличие от алюминия, магний характеризуется низкой пластичностью, поэтому в качестве конструкционного материала практически не рассматривается. Он обладает следующими свойствами:
- способность к образованию гидроокиси;
- высокая температура плавления;
- повышенная стойкость к коррозии;
- усиление механических показателей.
Самый легкий цветной металл – литий, который, как правило, используется для сплавов и незаменим для работ с оптикой, лазерами, а также производства анодов. При изготовлении электролитов для щелочных аккумуляторов применяется гидроксид, а в керамическом производстве – силикат и алюминат лития. Свойства этого элемента делают его весьма полезным для металлургической и военной промышленности, а также для медицины, фармацевтики, термоядерной отрасли.
Сплавы с участием легких цветных металлов
В чистом виде цветмет находит применение не так часто, как в качестве составляющих разнообразных сплавов. К примеру, хорошо знакомая бронза есть не что иное, как сочетание меди с алюминием, оловом, марганцем, свинцом и рядом других элементов. За счет хороших литейных характеристик материал широко используется для изготовления сантехнического оборудования (вентилей, кранов), осветительных устройств, предметов декора и прочих изделий.
Силумин также обладает высокими литейными характеристиками, сочетает свойства алюминия и кремния – пластичность, гибкость, твердость. Путем модифицирования эти механические характеристики силуминов можно заметно улучшить, благодаря повышению степени дисперсности кристаллов. Еще один сплав с алюминиевой основой – дюралюминий. Наряду с алюминием здесь присутствуют марганец, медь, кремний, магний и другие элементы, относящиеся к разным группам. Технические свойства дюралюминия повышаются посредством термической обработки.
Особенности сдачи легких сплавов
В настоящее время физические и юридические лица имеют возможность получить прибыль от сдачи цветмета в специализированные пункты приема. Стоимость лома определяется рядом факторов, среди которых качество материала, чистота его химического состава, категория и прочие параметры. Также имеют значение актуальные расценки на рынке, тарифы конкретной принимающей компании.
Формальная сторона вопроса сдачи любого лома, в том числе легких цветных металлов, имеет свою специфику. Право на такое мероприятие есть у каждого, но реализуется оно по-разному. Например, если сдача цветмета производится юридическим лицом – организацией, предприятием или представителем малого бизнеса (ИП), – то потребуется специальная лицензия. На физических лиц данное требование не распространяется, однако следует учитывать несколько правил:
- к приемке допускается только собственный лом (при наличии документов, подтверждающих право на владение);
- подлежащий сдаче цветмет должен входить в реестр материалов, принимаемых без лицензии;
- сдача лома нелегальным пунктам приема может иметь весьма неприятные последствия в соответствии с действующим законодательством.
Помимо сугубо меркантильного интереса сдача цветных металлов привлекательна с точки зрения экологии, сохранения запасов природных ресурсов. Переработанный лом снова идет на изготовление необходимой продукции, причем производство из вторсырья оказывается дешевле, чем при использовании руды. С учетом того, что потребность промышленности в ломе неуклонно растет, тогда как природные запасы сырья стремительно сокращаются, замкнутый производственный цикл является наиболее рациональным. Таким образом, каждый, кто сдает сдает лом цветмета, не только повышает собственное благосостояние, но и действует во благо общества в целом.
Медь | 310 руб./кг |
Бронза | 180 руб./кг |
Латунь | 180 руб./кг |
Нержавейка | 40 руб./кг |
Алюминий | 90-45 руб./кг |
АКБ б/у | 40 руб./кг |
Свинец | 85 руб./кг |
Кабель медный б/у (по выходу) | 320 руб./кг |
Кабель алюминиевый б/у (по выходу) | 70 руб./кг |
Кабель свинцовый б/у (по выходу) | 70 руб./кг |
ответим на вопросы
и рассчитаем сумму оплаты
Какие бывают виды и типы металлов и их сплавов
Твёрдость — устойчивость материала к проникновению другого.
- Прочность — сохранение формы, структуры и размера после воздействия динамической, статической и знакопеременной нагрузки.
- Упругость — изменение формы без нарушения целостности при деформации и возможность возвращения к первоначальному виду.
- Пластичность — удерживание полученной формы и целостности под воздействием сил.
- Износостойкость — сохранение наружной и внутренней целостности под воздействием продолжительного трения.
- Вязкость — удерживание целостности под увеличивающимся физическим воздействием.
- Усталость — число и период циклических воздействий, выдерживаемых металлом без изменения целостности.
- Жароустойчивость — стойкость к высоким температурам.
Первостепенным признаком металлов выступает отрицательный коэффициент проводимости электричества, который при понижении температуры повышается, а при повышении — частично или полностью теряется. Второстепенными признаками материалов являются металлический блеск и высокая температура плавления. Кроме того, некоторые типы металлов, являющихся соединениями, могут быть восстановителями при окислительно-восстановительных реакциях.
Металлические свойства взаимосвязаны, так как составляющие материала влияют на все остальные параметры. Металлы подразделяются на чёрные и цветные, но их классифицируют по многим признакам.
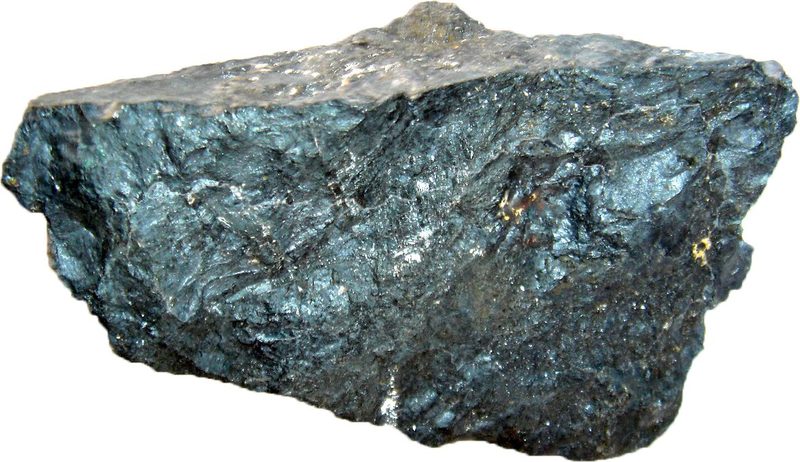
Металлы чёрной группы представлены сплавами железа с разным содержанием углерода и содержанием дополнительных химических элементов: кремнием, серой или фосфором. Популярными материалами выступают сталь и чугун. В стали содержится до 2% углерода. Ей характерна хорошая пластичность и высокие технологические показатели. В чугуне содержание углерода может достигать 5%. Свойства сплава могут отличаться с различными химическими элементами: с содержанием серы и фосфора повышается хрупкость, а с хромом и никелем чугун становится стойким к высоким температурам и коррозии.
Тяжёлые — кадмий, никель, олово, ртуть, свинец, цинк. В природных условиях они образуются в прочных соединениях.
- Лёгкие — алюминий, магний, стронций, титан и другие. Характеризуются невысокой температурой плавления.
- Благородные — золото, платина, родий, серебро. Для них свойственна повышенная стойкость к коррозии.
Цветные металлы отличаются небольшой плотностью, хорошей пластичностью, невысокой температурой плавления и преобладающими цветами (белым, жёлтым, красным). Из них изготавливается различная техника. Поскольку прочность материалов довольно низкая, их не используют в чистом виде. Из них производят лёгкие сплавы различного назначения.
Тяжёлые металлы
Материалы этой группы характеризуются внушительным атомным весом и плотностью, превышающей показатель у железа.
Большим спросом пользуется медь, которая выступает проводником электрического тока. Она отличается розовато-красным оттенком, маленьким удельным сопротивлением, хорошей теплопроводностью, небольшой плотностью, прекрасной пластичностью и устойчивостью к коррозии. В сфере техники используют сплавы меди: бронзу (с добавлением алюминия, никеля или олова) и латунь (с цинком). Бронзу применяют в производстве мембран, круглых и плоских пружин, червячных пар и разной арматуры. Из латуни изготавливают ленты, листы, проволоку, трубы, втулки, подшипники.
Группа тяжёлых металлов выступает одной из главных причин загрязнения окружающей среды. Токсичные вещества поступают в океаны через сточные воды с предприятий отрасли промышленности. Некоторые разновидности тяжёлой группы могут накапливаться в живых организмах.
Ртуть относится к высокотоксичным металлам для людей. При сжигании угля на электростанциях её соединения переходят в атмосферу, а затем преобразуются в осадки и попадают в водоёмы. Обитатели пресноводных и морских систем накапливают большое количество опасного вещества, что приводит к отравлениям или смерти людей.
Кадмий считается рассеянным и достаточно редким элементом, способным попадать в океан через сточные воды с металлургических предприятий. Это вещество в малом количестве есть в человеческом организме, но при высоком показателе он разрушает костную ткань и приводит к анемии.
Свинец в рассеянном состоянии присутствует почти везде. При избытке металла в организме человека наблюдаются проблемы со здоровьем.
Золото.
- Серебро.
- Платина.
- Родий.
Люди узнали о золоте ещё в эпоху каменного века. Самый дорогой металл в мире можно встретить в природе в виде самородков, в которых присутствует небольшое количество примесей. Также он встречается в сплавах с серебром.
Золото отличается теплопроводностью и очень низким сопротивлением. Из-за хорошей ковкости материал применяют в изготовлении ювелирных изделий.
Серебро идёт вторым по ценности после золота. В природе оно обычно встречается в качестве серебряной руды. Серебру характерны мягкость, пластичность, тепло- и электропроводность.
Платина, открытая в середине XX века, выступает редким материалом, который можно отыскать только в залежах различных сплавов. Её довольно трудно добывать. Ценность металла заключается в том, что он не подвергается воздействию кислот. При нагревании платина не изменяется в окраске и не окисляется.
Родий тоже относится к благородным металлам. Он обладает серебристым цветом с голубым отливом. Родий отличает устойчивость к химическим воздействиям и перепадам температур, но хрупкий металл портится под механическим воздействием.
Самый твёрдый из чистейших материалов в мире — это хром. Он относится к тугоплавким разновидностям и отлично поддаётся механической обработке. Другим твёрдым элементом выступает вольфрам. Он характеризуется высокой температурой плавления, теплоустойчивостью и гибкостью. Из него выковывают различные детали и изготавливают небольшие элементы, необходимые для осветительных приборов. Вольфрам часто присутствует в тяжёлых сплавах. Твёрдые металлы сложно не только добывать, но и просто найти на планете. В основном их содержат упавшие на Землю метеориты.
К самым мягким металлам относят калий, натрий, рубидий и цезий. Также в этой группе состоят золото, серебро, медь и алюминий. Золото присутствует в морских комплексах, осколках гранитов и человеческом организме. Внешние факторы способны разрушить ценный металл. Мягкое серебро применяют в изготовлении посуды и ювелирных украшений. Натрий широко используют практически в любой промышленной отрасли. Ртуть, выступающую самым мягким металлом в мире, применяют сельскохозяйственной и химической промышленности, а также электротехнике
ЛЕГКИЕ КОНСТРУКЦИОННЫЕ МЕТАЛЛЫ
К наиболее распространенным способам классификации цветмета по его физико-химическим свойствам относится распределение на семь групп, среди которых выделяются так называемые тяжелые и легкие цветные металлы. Данное условное определение основано на показателе плотности материала. В основной список входят алюминий, магний, титан, литий, олово, бериллий. К этой же группе относятся кадмий, таллий, галлий, висмут, индий и другие элементы. Производство легких сплавов является крайне энергозатратным, поэтому предприятия, специализирующиеся на этой области металлургии, размещаются непосредственно вблизи источников дешевой энергии.
Специфические особенности
Несмотря на принадлежность к общей группе, разные легкие цветные металлы имеют специфические свойства, отличающие их друг от друга, а также обуславливающие ценность конкретного материала и область его применения. Чтобы лучше понять эти нюансы, стоит подробнее рассмотреть основных представителей данного вида цветмета.
Пожалуй, наиболее типичным примером легкого цветного металла, хорошо знакомого самому обширному кругу пользователей, является алюминий. Материал пластичен и легко обрабатывается, за счет чего чрезвычайно популярен в широчайшем спектре производств – от космической и авиационной промышленности до изготовления кухонной посуды. Окисная пленка надежно защищает поверхность алюминиевых изделий от негативного воздействия окружающей среды, агрессивных веществ. К главным свойствам относятся:
- высокая тепло- и электропроводность;
- стойкость к коррозии;
- высокая пластичность;
- малая плотность.
В отличие от алюминия, магний характеризуется низкой пластичностью, поэтому в качестве конструкционного материала практически не рассматривается. Он обладает следующими свойствами:
- способность к образованию гидроокиси;
- высокая температура плавления;
- повышенная стойкость к коррозии;
- усиление механических показателей.
Самый легкий цветной металл – литий, который, как правило, используется для сплавов и незаменим для работ с оптикой, лазерами, а также производства анодов. При изготовлении электролитов для щелочных аккумуляторов применяется гидроксид, а в керамическом производстве – силикат и алюминат лития. Свойства этого элемента делают его весьма полезным для металлургической и военной промышленности, а также для медицины, фармацевтики, термоядерной отрасли.
Технология производства лития
Производство самого легкого металла в мире сводится к разложению его природных соединений. Это достаточно трудоемкая процедура ввиду большого количества составных элементов. Содержание лития в добываемом сырье в среднем составляет 21 грамм на одну тонну. В промышленном производстве используют три метода разложения соединений лития: известковый, сульфатный и сернокислотный. Первые два подразумевают спекание руды с оксидом/карбонатом кальция или сульфатом калия.
Протекает процедура при температуре 250-300 градусов. Затем полученную массу обрабатывают водой, получая карбонат или сульфат лития. После этого проводится процедура хлорирования с целью получения хлорида лития. И, наконец, окончательную процедуру разделения проводят при помощи электролиза расплава в присутствии хлорида калия или бария, которые понижают температуру плавления литиевого хлорида. Чистый металл оседает на катоде, откуда его можно собирать для дальнейшей переработки.
Сернокислотный способ подразумевает растворение руды в серной кислоте с образованием сульфата лития. Дальнейшая процедура протекает по указанной выше схеме. Самый легкий металл применяется для производства эффективных полупроводников в сплавах с другими металлами, из него изготавливают аноды, используемые затем в процедурах электролиза, литий входит в состав ракетного топлива, в металлургии применяется в качестве сильного восстановителя менее активных металлов. В качестве различных соединений литий используется в производстве продукции для многих отраслей промышленности и народного хозяйства.
Сплавы с участием легких цветных металлов
В чистом виде цветмет находит применение не так часто, как в качестве составляющих разнообразных сплавов. К примеру, хорошо знакомая бронза есть не что иное, как сочетание меди с алюминием, оловом, марганцем, свинцом и рядом других элементов. За счет хороших литейных характеристик материал широко используется для изготовления сантехнического оборудования (вентилей, кранов), осветительных устройств, предметов декора и прочих изделий.
Силумин также обладает высокими литейными характеристиками, сочетает свойства алюминия и кремния – пластичность, гибкость, твердость. Путем модифицирования эти механические характеристики силуминов можно заметно улучшить, благодаря повышению степени дисперсности кристаллов. Еще один сплав с алюминиевой основой – дюралюминий. Наряду с алюминием здесь присутствуют марганец, медь, кремний, магний и другие элементы, относящиеся к разным группам. Технические свойства дюралюминия повышаются посредством термической обработки.
3.3. Легкие сплавы
Металлы, обладающие малой плотностью, называют легкими металлами. Из широко используемых к ним относятся алюминий (плотность 2 700 кг/м3), магний (1 740), бериллий (2 848) и титан (4 505). Из этих металлов получают легкие сплавы, а также их применяют в качестве легирующих добавок к другим сплавам. Из легких металлов и сплавов делают детали и устройства воздушного и водного транспорта, в которых большая масса является критичной для работы конструкции. Легкие металлы и сплавы характеризуются высокой удельной прочностью, т. е. высоким отношением механических свойств к их плотности. Так, алюминиевые сплавы в литом состоянии по удельной прочности превосходят все другие литейные сплавы, а в деформированном состоянии равноценны конструкционным высокопрочным сталям.
К легким конструкционным сплавам относятся алюминиевые, бериллиевые, магниевые и титановые сплавы, у которых удельная прочность выше, чем, например, у конструкционных сплавов на основе железа или никеля. Так, при одинаковой прочности дюралюминий в 3 раза легче котельной стали и его удельная прочность примерно в 3 раза выше, чем у стали.
Алюминий — основа многих легких сплавов, в которые легирующие добавки (медь, кремний, магний, цинк, марганец) вводят, главным образом, с целью повышения прочности основы.
Основные сплавы алюминия — дюралюмины и силумины, по-лучившие широкое применение в авиационной, автомобильной, судостроительной, тракторной промышленности и приборостроении. Эти сплавы подразделяют на обрабатываемые давлением (деформируемые) и литейные. Дюралюмины — сплавы алюминия с добавками 3,8…5,2 % меди, 0,4… 1,8 % марганца и 0,4… 1,0 % магния. Кроме указанных элементов в дюралюмины могут входить и другие (например, никель) улучшающие его механические характеристики элементы. Силумины — это литейные сплавы алюминия с кремнием.
Алюминиевые литейные сплавы по физико-химическим свойствам можно разделить на несколько групп, исходя из содержания определяющих их основные характеристики легирующих элементов.
Алюминиевые сплавы с высоким содержанием кремния (5 % и более) обладают высокой литейной способностью — повышенной жидкотекучестью, малой усадкой, отсутствием трещин в горячем состоянии и т.д. (это сплавы АЛ2, AJI4, АЛ9 и др.).
Алюминиевые сплавы с высоким содержанием магния (4 % и более) имеют самую малую плотность из всех литейных алюминиевых сплавов, коррозионно-стойкие и сравнительно высокопрочные (это сплавы AJ18, АМг5, АМгб).
Алюминиевые сплавы с высоким содержанием меди (4 % и более) особыми свойствами не обладают — значительная плотность, низкие коррозионная стойкость и жидкотекучесть, поэтому пригодны для изготовления изделий неответственного назначения (это сплавы AJT7, AJ112, AJI19).
Алюминиевые сплавы с высоким содержанием цинка (10… 12 %) и кремния (6…8%) характеризуются тем, что хорошо заполняют литейную форму, дают чистую поверхность, не требуют специальной термической обработки (это сплав АЛ11 и др.).
Многофазные сплавы с гетерогенной (неоднородной) и устойчивой структурой (сплавы типа АЛ 1) являются жаропрочными и используются для деталей, работающих при повышенной температуре. При этом, чем выше жаропрочность сплава, тем хуже его технологические свойства.
Из деформируемых алюминиевых сплавов можно отметить, например, малолегированные и термически не упрочняемые сплавы типа АМц, АМг и др. Сюда относят сплавы с постоянными примесями железа и кремния, иногда с добавкой титана. Сплавы, содержащие 2…7% магния, образуют семейство материалов типа магнолит, они имеют высокую коррозионную стойкость, пластичны, хорошо свариваются. Основной способ упрочнения — на-гартовка. Из этих сплавов делают профили, трубы, листы, прутки и др. Сплавы типа дюралюмин (Д16) применяют в закаленном и состаренном состояниях, они работоспособны при температуре до 200 °С, поэтому эти сплавы используют для производства конструкций, работающих при повышенных температурах. Если из этого материала сделать заклепки, то время их расклепывания ограничивается малым временем после закалки.
Наряду с дюралюминами и силуминами используют и другие сплавы на основе алюминия — авиаль и магналии.
Авиаль — сплав на основе алюминия, содержащий до 0,45 % магния, 0,5… 1,2% кремния, 0,2…0,6% меди, 0,15…0,35% марганца или хрома. Этот сплав обладает высокой пластичностью и удовлетворительной атмосферной коррозионной стойкостью. Термической обработкой (закалкой и старением) авиаль упрочняют. Так как сплав обладает достаточной пластичностью и хорошо обрабатывается давлением, из него изготовляют детали сложной формы (лопасти винтов вертолетов).
Магналии — сплавы на основе алюминия, легированные 1… 13 % магния, — бывают литейные (4… 13% магния) для изготовления сложных фасонных отливок и деформируемые (1…7% магния), хорошо сваривающиеся и имеющие высокие показатели по коррозионной стойкости и пластичности. Такие сплавы используют в судостроении и ракетостроении.
Бериллий и бериллиевые сплавы
становятся все более востребованными в связи с бурным развитием специальной техники — ракетостроения, авиации, созданием космических и глубоководных аппаратов и других изделий, так как данные материалы обладают комплексом ценных свойств.
Даже при небольших добавках бериллия в Цветные металлы или в стали их свойства значительно улучшаются. Например, сплав меди с 1…5% бериллия (бериллиевая бронза) обладает прочностью на разрыв большей, чем многие легированные стали. В отличие от чистого бериллия такой материал хорошо обрабатывается механическими способами, из него можно изготовить ленты толщиной 0,1 мм. Бериллиевая бронза используется для изготовления пружин, рессор, амортизаторов, подшипников, шестерен и других изделий, от которых требуется большая прочность, хорошая сопротивляемость усталости и коррозии, сохранение упругости в широком интервале температур.
Стали, легированные бериллием, обладают повышенными прочностью, коррозионной стойкостью и свариваемостью. По сравнению с другими сталями сталь, легированная бериллием, проявляет стойкость к воздействию морской воды, нефти, мазута и других видов углеводородного топлива. Подобные стали находят применение в судостроении и при изготовлении глубоководных аппаратов.
Содержащие бериллий сплавы используют в разных областях науки и техники, по больше всего в ядерной физике, авиации, ракетостроении, космических устройствах, машиностроении, медицине. Например, масса крыла самолета из бериллия меньше массы аналогичного крыла из стали на 60 %, а из титана на 30 %. Из бериллиевых сплавов делают обтекатели самолетов, детали турбореактивных и турбовинтовых двигателей, передние кромки крыльев сверхзвуковых самолетов, лонжероны, тормозные диски колес и рули наведения. Использование данных сплавов для космических устройств обусловлено сочетанием высокой удельной прочности с большой удельной жесткостью. У бериллия жесткость в пределах упругих деформаций в 6 раз превышает жесткость других конструкционных материалов.
Улучшить свойства металлов можно как путем легирования бериллием на этапе получения сплава, так и поверхностным насыщением изделия бериллием по аналогии с цементацией. Технология не сложная: стальную деталь помещают в бериллиевый порошок и выдерживают в нем при температуре 900… 1 100°С в течение 10… 15 ч. В результате диффузии на поверхности стальной детали образуется слой толщиной 0,15…0,40 мм из соединения бериллия с железом и углеродом. Этот слой делает сталь жаро-стойкой, устойчивой к морской воде, азотной кислоте, кроме того, хорошо работающей на износ.
Используя бериллиевые волокна и синтетическую бумагу, можно изготовить новый композиционный материал — это специальная жаропрочная бумага (работает при воздействии температуры до 2 200°С), которая не боится термических ударов (резкой смены температур), химически инертна и обладает высокими тепло-, звуко- и электроизоляционными свойствами. С учетом указанных качеств ее применяют в космических кораблях, реактивных двигателях, газовых турбинах и ракетах.
Весьма ценным является керамический материал из оксида бериллия (брокерит, бромеллит), обладающий одновременно высокими диэлектрическими и теплопроводными свойствами и в то же время довольно легкий — его плотность равна 2 957 кг/м3, а теплопроводность составляет примерно 50 % теплопроводности меди.
Бериллий обладает высокой теплотворной способностью — при сгорании 1 кг бериллия выделяется 60 000 кДж теплоты, поэтому его используют в качестве добавки в ракетное топливо. Кроме металлического бериллия добавками служат соединения бериллия, например, гидрид бериллия и некоторые бериллийорганические вещества.
Наряду с достоинствами бериллий и его соединения имеют и недостатки, главным из которых является высокая токсичность (ядовитость). Особенно вредны мелкие частицы соединений бериллия, и чем выше их дисперсность (т.е. чем они мельче), тем они токсичнее. Уровень токсичности зависит от температуры спекания — оксид бериллия (бромеллит), спеченный при температуре 1600°С, менее вреден, чем тот же материал, но созданный при температуре 500 °С. Попав в живой организм, бериллий соединяется с костной и легочной тканями и разрушает их. Кроме того, он вызывает сильные воспалительные заболевания кожи — дерматиты. Предельные допустимые концентрации (ПДК) оксида бериллия в воздухе для работающих очень малы и составляют одну тысячную долю микрограмма на один кубический метр.
Магний с алюминием (до 11 %) и другими металлами (марганец до 2,5%, цинк 2. 3%, медь 0,25%, кремний 1,5% и титан) образует сверхлегкие сплавы, изделия из которых для авиапромышленности получают преимущественно обработкой давлением с подогревом до 4ОО…430°С и литьем.
Магниевые сплавы
закаливают и подвергают старению, но эффект термической обработки по сравнению с алюминиевыми сплавами меньше. От коррозии магниевые сплавы защищают оксидированием и покрытием лаками. Магниевые сплавы разделяют на литейные и деформируемые. К литейным относятся сплавы MJ12 (1 …2 % марганца), МЛ6 (9,0… 10,2 % алюминия, 0,6… ] ,2 % цинка, 0,15…0,50% марганца и др.), к деформируемым — сплавы МА1 (1,3…2,5% марганца), МА5 (7,8…9,2% алюминия, 0,15…
0,50% марганца, 0,2…0,8% цинка и др.).
Достоинством сплава MJ12 является хорошая коррозионная стойкость и свариваемость, термической обработке он не подвергается. Литейные свойства этого сплава низкие, поэтому из него отливают бензобаки, бензомасляную арматуру и другие детали простой конфигурации. Сплав MJ16 имеет хорошие литейные свойства, отливки из него получают литьем в землю, в кокиль и под давлением. Свариваемость сплава MJT6 удовлетворительная, а коррозионная стойкость ниже по сравнению с другими сплавами. Из этого сплава изготовляют тяжелонагруженные детали двигателей, так как сплав имеет повышенный предел текучести. Литейные сплавы для проведения литья нагревают до температуры 700… 800 °С, кристаллизация происходит в интервале температур 600…440°С, линейная усадка при этом составляет в среднем 1,2… 1,4 %.
Магниевые деформируемые сплавы изготовляют в виде листов, прутков, профилей, плит, поковок в термообработанном и необработанном виде. Фасонные отливки, как правило, отжигают, закаливают и старят.
по распространенности в недрах занимает четвертое место после алюминия, железа и магния. Этот легкий металл (плотность 4 540 кг/м3) плавится при температуре около 1 660 °С, легко образует соединения с кислородом, азотом, углеродом — оксиды, нитриды, карбиды, которые довольно твердые п тугоплавкие. Титан имеет высокие прочность и коррозионную стойкость. В виде добавок входит в состав многих металлических материалов, образует жаропрочные сплавы, а его карбиды являются одними из основных составляющих твердых сплавов. Этот металл хорошо обрабатывается резанием, при нагреве до 900°С куется, а при температуре около 1 000 °С прессуется в прутки разных профилей и трубы, прокатывается в холодном состоянии, но быстро упрочняется и требует частых отжигов в вакууме (гелии), после которых становится пластичным. Сваривают титан аргон но-дуговой сваркой.
Промышленные сплавы титана содержат, например, 8 % марганца, или по 4 % марганца и алюминия, или по 2 % железа, хрома и молибдена, или 3 % алюминия и 5 % хрома и др. Главными достоинствами титановых сплавов являются высокая жаростойкость, жаропрочность, коррозионная стойкость, значительное электрическое сопротивление и благоприятная удельная прочность. С учетом этого титановые сплавы используют в авиационной промышленности. Из титановых сплавов делают детали обивки фюзеляжа, крыльев, хвостового оперения и др. В турбореактивных двигателях из них изготовляют моторные рамы, диски и лопатки компрессоров, распорные кольца и другие детали. Поплавки гидросамолетов производят из титанового сплава, обладающего стойкостью в морской воде.
Рис. 3.1. Диаграмма изменения пределов прочности о„ цветных металлов и сплавов в зависимости от наклепа (степени обжатия): 1,2 — алюминий и кольчугалюминий; 3, 10 — медь и никель; 4, 9 — никелины с разным содержанием компонентов; 5, 7 — алюминиевая и фосфористая бронзы; 6 — константан; 8 — латуни
Корпуса подводных лодок и глубоководных аппаратов делают из титановых сплавов, как и гребные винты, трубопроводы, насосы и др. Титан используют в химической (трубопроводы, резервуары для агрессивных сред), инструментальной (карбиды титана в твердых сплавах), электротехнической (сплавы с высоким электросопротивлением), медицинской (внутренние протезы) и других отраслях промышленности.
Обрабатывать легкие конструкционные сплавы можно в горячем и холодном состоянии. По мере увеличения степени деформации при холодной обработке происходит постепенное повышение твердости и прочности металла. Для получения дальнейшей деформации требуется все большее усилие. При этом металл становится более прочным, менее пластичным, получает так называемый наклеп.
Наклеп и нагартовка (от нем. hart — твердый) — явления повышения твердости и прочности — понятия, равнозначно обозначающие повышение механических свойств металлов в результате их обработки давлением (штамповка, ковка, прокатка, волочение, выглаживание роликами, дробью и др.).
Изменения прочности цветных металлов в зависимости от наклепа приведены на рис. 3.1. Увеличение ов при наклепе показано для алюминия и кольчугалюминия, меди и никеля, никелинов с разным содержанием компонентов, алюминиевой и фосфористой бронз, константана, латуни.
Особенности сдачи легких сплавов
В настоящее время физические и юридические лица имеют возможность получить прибыль от сдачи цветмета в специализированные пункты приема. Стоимость лома определяется рядом факторов, среди которых качество материала, чистота его химического состава, категория и прочие параметры. Также имеют значение актуальные расценки на рынке, тарифы конкретной принимающей компании.
Формальная сторона вопроса сдачи любого лома, в том числе легких цветных металлов, имеет свою специфику. Право на такое мероприятие есть у каждого, но реализуется оно по-разному. Например, если сдача цветмета производится юридическим лицом – организацией, предприятием или представителем малого бизнеса (ИП), – то потребуется специальная лицензия. На физических лиц данное требование не распространяется, однако следует учитывать несколько правил:
- к приемке допускается только собственный лом (при наличии документов, подтверждающих право на владение);
- подлежащий сдаче цветмет должен входить в реестр материалов, принимаемых без лицензии;
- сдача лома нелегальным пунктам приема может иметь весьма неприятные последствия в соответствии с действующим законодательством.
Помимо сугубо меркантильного интереса сдача цветных металлов привлекательна с точки зрения экологии, сохранения запасов природных ресурсов. Переработанный лом снова идет на изготовление необходимой продукции, причем производство из вторсырья оказывается дешевле, чем при использовании руды. С учетом того, что потребность промышленности в ломе неуклонно растет, тогда как природные запасы сырья стремительно сокращаются, замкнутый производственный цикл является наиболее рациональным. Таким образом, каждый, кто сдает сдает лом цветмета, не только повышает собственное благосостояние, но и действует во благо общества в целом.
Биметаллы
Биметаллы – это вид композитного материала, состоящий из двух или нескольких разнородных металлов сцепленных между собой.
Они применяются для экономии дорогих цветных и ценных металлов, а также приданию материалам новых свойств. При этом слой более дешевого металла, который воспринимает силовую нагрузку, называют основным, а более дорогого, который обеспечивает специальный свойства, – плакирующим.
В качестве основного слоя используют сталь, а в качестве плакирующего специальные сплавы, цветные и благородные металлы.
Рис. 97. Виды биметаллов: а) лист из коррозионностойкого биметалла; б) труба из коррозионностойкого биметалла; в) вкладыш подшипника из антифрикционного биметалла; г) лента пилы из износостойкого биметалла; в) термореле с пластинкой из термобиметалла; е) провод из электробиметалла
В зависимости от материала плакирующего слоя и назначения различают следующие виды биметаллов:
- Коррозионностойкие. Основной слой коррозионностойкого биметалла состоит из низкоуглеродистой или низколегированной стали, а плакирующий из нержавеющей стали (например 12Х18Н10Т, 08Х13), меди, никеля или их сплавов, алюминия. Такие биметаллы применяются в виде толстых и тонких листов (рис. 97, а) или труб (рис. 97, б) в химической, нефтеперерабатывающей, пищевой промышленности и судостроении.
- Антифрикционные. Антифрикционные биметаллы применяются в подшипниках скольжения (рис. 97, в). В качестве плакирующего слоя такого биметалла используются бронза или алюминий, которые обладают хорошими антифрикционными свойствами, но низкой прочностью, а в качестве основного слоя используется низкоуглеродистая сталь. Такие биметаллы выпускаются в виде лент, которые используются для изготовления вкладышей подшипников.
- Износостойкие и инструментальные биметаллы. Применяются для изготовления режущего инструмента (ножей, пил (рис. 97, г) и т.д.) В качестве основного слоя используется низкоуглеродистая сталь, а в качестве плакирующего слоя используют инструментальные легированные хромом стали (например Х12М, 9Х5Ф и т.д.) или твердые сплавы.
- Термо-биметаллы. Для таких производства таких биметаллов один слой состоит из металла с большим температурным коэффициентом линейного расширения (цветные металлы, сплавы 24НХ, Л90, 75ГДН), а второй слой из пассивных металлов, которые практически не расширяются (инвар – сплав железа и никеля). Полоса, изготовленная из такого материала изгибается под действием температуры из-за разного коэффициента линейного расширения двух металлов. Такие биметаллы используются для термометров, терморегуляторов (рис. 97, д), защитных реле.
- Электропроводные. В таких биметаллах более электропроводный материал располагается на поверхности, а основой является мене электропроводный металл или сталь. В качестве электропроводного слоя в основном используется медь, реже – алюминий. Такие биметаллы используются в линиях электропередач в северных районах (рис. 97, е) и в качестве контактного провода на железной дороге.
Способы получения биметаллов
Среди способов получения биметаллов, распространены следующие:
- одновременная прокатка;
- одновременное прессование или волочение;
- налив расплава одного металла на другой, более тугоплавкий;
- комбинированное литье;
- покрытие гальваническим способом;
- газотермическое напыление;
- наплавка;
- плакирование взрывом.
Рассмотрим основные способы получения биметаллов подробнее.
Комбинированное литье
Способ комбинированного литья (рис. 98) заключается в следующем: в изложницу для слитков закладывают перфорированные разделительные листы, отмечающие положение будущей плоскости соединения между металлами А и Б, затем заливают металлы А и Б одновременно из двух ковшей через две воронки, контролируя равенство высот зеркала жидкого металла в обеих частях изложницы.
Рис. 98. Способы последовательной отливки металлов: 1 – форма; 2 – залитый металл; 3 – разливочная воронка; 4 – перегородка; 5 – желоб; 6 – заливаемый металл; 7,8 – кристаллизатор; 9,10 – металл (составляющие биметалла).
а) – способ последовательной отливки металлов с применением выдвижной перегородки;
б) – способ последовательной отливки металлов с применением схемы расположения кристаллизаторов при отливке трехслойной заготовки.
в) – способ последовательной отливки металлов с применением схемы расположения кристаллизаторов при отливке двухслойной заготовки.
г) – способ последовательной отливки металлов с применением схемы расположения кристаллизаторов при отливке двухслойной цилиндрической заготовки.
Затем биметаллический слиток прокатывают на плакированные листы или фасонные профили. Возможна заливка более двух металлов. Разновидностью способа является заливка одного жидкого металла на слой твердого, который предварительно помещен в изложницу (рис. 99).
Рис. 99. Производство биметаллов заливкой: а) однослойный биметалл; б) двухслойный биметалл; в) трехслойный биметалл. 1- изложница; 2- твердый слой металла; 3 – жидкий металла
Пакетная прокатка
По способу пакетной прокатки плакированные листы получают путем прокатки собранных и сваренных многослойных пакетов (рис. 100).
Рис. 100. Схема составления пакетов биметалла перед прокаткой: а – конструкция одинарного; б – двойного симметричного; в – двойного несимметричного; г – тройного пакета: 1 – пакет; 2 – свариваемая заготовка; 3 – планка; 4 – технологическое сварное соединение; 5 – поверхности свариваемых заготовок
В зависимости от назначения, расположение и количество слоев может быть различным (двух-, трех- и четырехслойные пакеты). Листы могут быть с одно- и двухсторонним плакированием.
Сущность метода пакетной прокатки заключается в том, что основной и плакирующий металл собираются вместе в пакет, который обваривают герметичными швами и заполняют инертным газом.
Затем, пакет перед прокаткой нагревают до температур 1150…1250 °С, при который происходит растворение и восстановление окислов на всех поверхностях герметичного объема.
Последующая прокатка с величиной обжатия не менее 60% приводит к сварке основного металла с плакирующим слоем. Прокатывают такой пакет на обычных толстолистовых
станах.
Холодная сварка прокаткой
Холодную сварку прокаткой (рис. 101) применяют для получения двух- или трехслойных биметаллов, состоящих из стальной основы и плакирующих слоев из цветных металлов, например сталь + медь, сталь + латунь, медь + алюминий, алюминий + титан, алюминий + сталь + алюминий.
Рис. 101. Холодная сварка прокаткой
Для получения доброкачественного соединения слоев в биметалле требуется значительная деформация при сварке прокаткой и чистота соединяемых поверхностей, причем особенно важно отсутствие органических веществ.
При сварке прокаткой соединение образуется в условиях принудительного деформирования и малой длительности взаимодействия.
Холодная сварка прокаткой производится по следующей схеме:
- подготовка поверхности прокатываемых заготовок (травление, зачистка и т.д.);
- холодная прокатка на двухвалковом стане с обжатием 45…50% за один проход;
- промежуточный отжиг биметаллического проката в печах при температуре 320…330 ºС в течении 1 часа;
- холодная прокатка, калибровка и правка полос;
- окончательный отжиг биметалла при температуре 450…460 ºС в течении 3 часов.
Плакирование также производят накаткой порошка на полосу, а также путем прокатки порошковой ленты.
Прессование биметаллов
Самый простой способ прессования биметаллов заключается в горячем выдавливании через отверстие матрицы составной заготовки, имеющей круглое или трубное сечение с концентрическим расположением слоёв. Заготовка может быть изготовлена из различных комбинаций сталей, металлов или сплавов.
Рис. 102. Схема прессования биметаллических заготовок: а) – труба, б) – пруток. 1 – пресс-штемпель; 2 – внутренняя втулка контейнера;3 – пресс-шайба; 4 – контейнер; 5 – игла; 6 – прессуемая труба (пруток); 7 – матрица; 8 – матрицедержатель; 9 – обойма матрицедержателя; 10 – запорный клин.
Для осуществления этого процесса можно использовать различные горизонтальные или вертикальные прессы, применяемые для прессования прутков, профилей или труб из цветных металлов и сталей. На рис. 102 приведена принципиальная схема процесса прессования биметаллического прутка и биметаллической трубы.
Волочение
Совместное холодное волочение является методом получения биметаллической проволоки сталь + алюминий или сталь + другие цветные металлы. На стальную проволоку (сердечник) со специально подготовленной поверхностью надевают рубашку в виде трубки, которая может быть бесшовной или в виде сформованной в трубку ленты. Если материал рубашки является высокопластичным, то при совместной пластической деформации в волоке происходит достаточно прочное соединение двух металлов.
Полученная таким образом биметаллическая проволока может быть использована в качестве проводника электрического тока или как коррозионностойкая проволока для различных целей.
Плакирование взрывом
Соединение двух металлов взрывом применяют для таких пар материалов, соединить которые другими способами плакирования трудно (из-за нерастворимости друг в друге, большом различии в сопротивлении деформации и т.д.) или же для изготовления изделий специального (часто военного) назначения. Для этого способа характерно применение основного металла и плакирующего материала в холодном состоянии. Плакирующий лист располагают под небольшим углом к основе, или просто накладывают один на другой. Затем устанавливают бортики и на поверхность плакирующего листа помещают взрывчатое вещество с детонатором (рис. 103).
Рис. 103. Схема плакирования сваркой взрывом плоских поверхностей: 1 – пластина плакирующего металла; 2 – основной металл; 3 – основание; 4 – взрывчатое вещество; 5 – детонатор
При взрыве, во время соударения пластин возникает струя металла, выходящая с поверхностных слоев основного и плакирующего материала. Вместе с ней удаляется и загрязнение, что способствует образованию очень чистых поверхностей при соединении материалов. Взрывы производят в специально отведенных для этого бункерах. После взрыва производится контроль соединения, обрезка краев и обработка поверхности готового биметалла.
Наплавка
Основные способы дуговой наплавки приведены на (рис. 104). Автоматическая наплавка под флюсом – наиболее распространенный и хорошо изученный процесс, весьма эффективный при изготовлении биметаллических деталей. При дуговой наплавке под флюсом сварочная дуга между электродом и изделием горит под слоем сухого гранулированного флюса, одновременно плавится сварочная проволока, основной металл и флюс.
Рис. 104. Получение биметаллов методом наплавки: 1 – присадочный материал; 2 – защитные покрытия; 3 – основной
металл; 4 -наплавленный металл; а) графитовым электродом; б) ручной дуговой покрытым электродом с легирующим покрытием; в) неплавящимся вольфрамовым электродом в защитных инертных газах; г) плавящимся электродом в защитных газах; д) автоматическая дуговая плавящейся электродной проволокой под флюсом; е) плавящейся лентой; ж) расплавлением плазменной струей плазмотрона наплавочного материала; з) электрошлаковая наплавка
Металл наплавленного валика, полученного под флюсом, состоит из расплавленного присадочного металла и переплавленного основного. Использование флюса обеспечивает уменьшение разбрызгивания и угара металла. Для уменьшения проплавления основного металла используют многоэлектродную наплавку или ведут процесс с колебанием электрода поперек шва.
Газотермическое напыление
Это процесс получения покрытия из нагретых и ускоренных частиц материала с использованием высокотемпературного газового потока, при соударении которых с основой или напыленным материалом идет их соединение за счет сваривания, адгезии и механического сцепления. По энергетическим признакам методы газотермического нанесения покрытий подразделяются на газопламенный, детонационный, плазменный и электродуговой. Эти методы отличаются типом источника энергии, расходуемой на нагрев и ускорение материала, создающего покрытие.
Источник: Скляр В. О. Инновационные и ресурсосберегающие технологии в металлургии. Учебное пособие. – Донецк.: ДонНТУ, 2014. – 224 с.
Источник https://elton-zoloto.ru/metally-i-splavy/chto-otnositsja-k-legkim-metallam.html
Источник https://kamuflyzh.ru/o-materialah/legkie-splavy-metallov.html
Источник https://metallolome.ru/bimetally/